Backflow Prevention
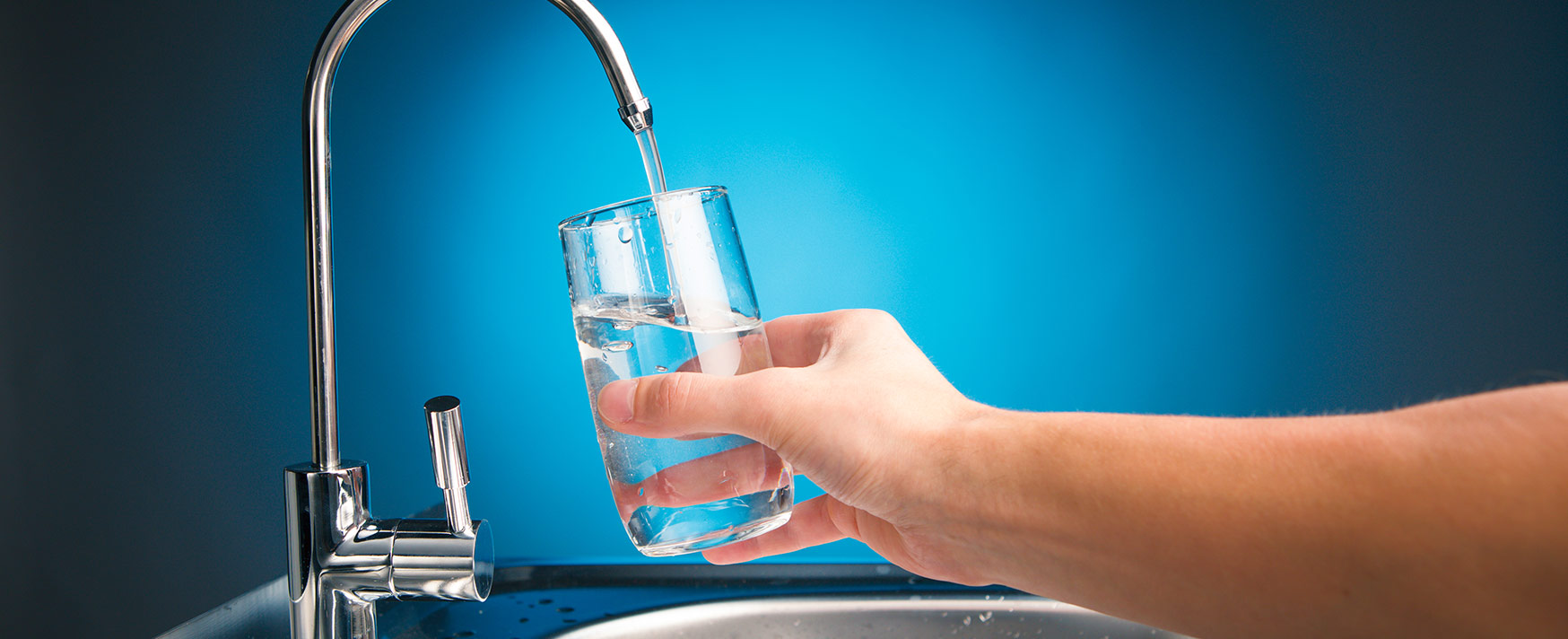
Backflow Prevention Testing
Keeping the community and its waters healthy requires a frequent backflow prevention device inspection (RPZ). This is a specialised valve designed to prevent potentially contaminated water from flowing back into the water supply. And when it comes to backflow prevention testing, Sydney and Gold Coast businesses can be sure they’re getting the best and most efficient service from Watertight.
Periodic maintenance and testing of a backflow device is a strict requirement from the local water authority for all property owners with one of these devices installed. Across Australia, every property is required to have a backflow device installed and tested annually where the property’s water meter is larger than 25 mm.
As a property owner with a backflow prevention device you are responsible for ensuring that the correct type of valve has been installed and that it is maintained correctly by a fully accredited backflow plumber. It is the responsibility of the property owner to ensure that a certificate of compliance is submitted when a new backflow valve has been installed or the yearly testing certification has been carried out. It might sound intimidating, but in reality a backflow prevention device inspection or the installation of a new device couldn’t be simpler; just give our friendly team at Watertight Group a call, and we’ll walk you through the compliance and regulatory requirements.
Backflow prevention device inspection with the Watertight Group: our process
We offer a full suite of backflow device services, ranging from the installation of new valves to the maintenance of existing devices.
If you need a new backflow prevention device (for example, you’re moving into a new property), Watertight Group can advise you on the property’s hazard rating and install the correct device for your property within the greater Sydney area to ensure you comply with Sydney Water’s backflow device requirements.
For existing properties, when we come out to conduct a backflow prevention device inspection, we will conduct a range of tests to ensure that your backflow prevention device will stop the reverse flow of water from unsafe sources into your drinking supply system.
Backflow testing is vital to ensure that the RPZD is operating correctly. If it is, there will be clean drinking water supplied to your property with no contaminants. However, if it is not working well or faulty, contamination of your drinking water may occur. This impacts the safety of the water quality on your property and could cause harm or in some cases even death. It’s extremely important to ensure you have regular backflow testing to prevent contamination.
Get on top of your mandatory annual compliance inspection
It’s important to know that the backflow prevention device inspection is, in fact, mandatory. You’ll need to have them checked by a fully certified plumber once per year. Your local water authority may audit your property to ensure ongoing compliance with the Backflow Prevention Containment Policy.
Watertight Group will ensure we test your device thoroughly. Our highly experienced team are fully certified to conduct maintenance and yearly certification testing of all types of backflow prevention devices. We will ensure all your backflow prevention devices are functioning correctly and will issue you with the Certificate of Compliance and the Backflow Prevention Device Inspection and Maintenance Report for each device.
As an additional service to our customers, at no additional charge Watertight Group will submit the certification reports from our backwater prevention device inspection of your property to Sydney Water or your relevant water authority (we also provide this service in the Sydney CBD, Greater Sydney areas, Illawarra region, ACT, Goulburn, Central Coast and other regional NSW areas), the same day of commissioning or testing the device to ensure your compliance with their respective requirements.
As part of our quality guarantee you will never have to worry about forgetting your annual test again. Watertight Group will send you a reminder annually for device testing and arrange a convenient time to carry out testing ensuring we do not hold up the productivity of your business, school, entertainment, health, aged care or corporate facility.
For more information on backflow prevention (RPZ), contact us or give us a call on 1300 745 758.